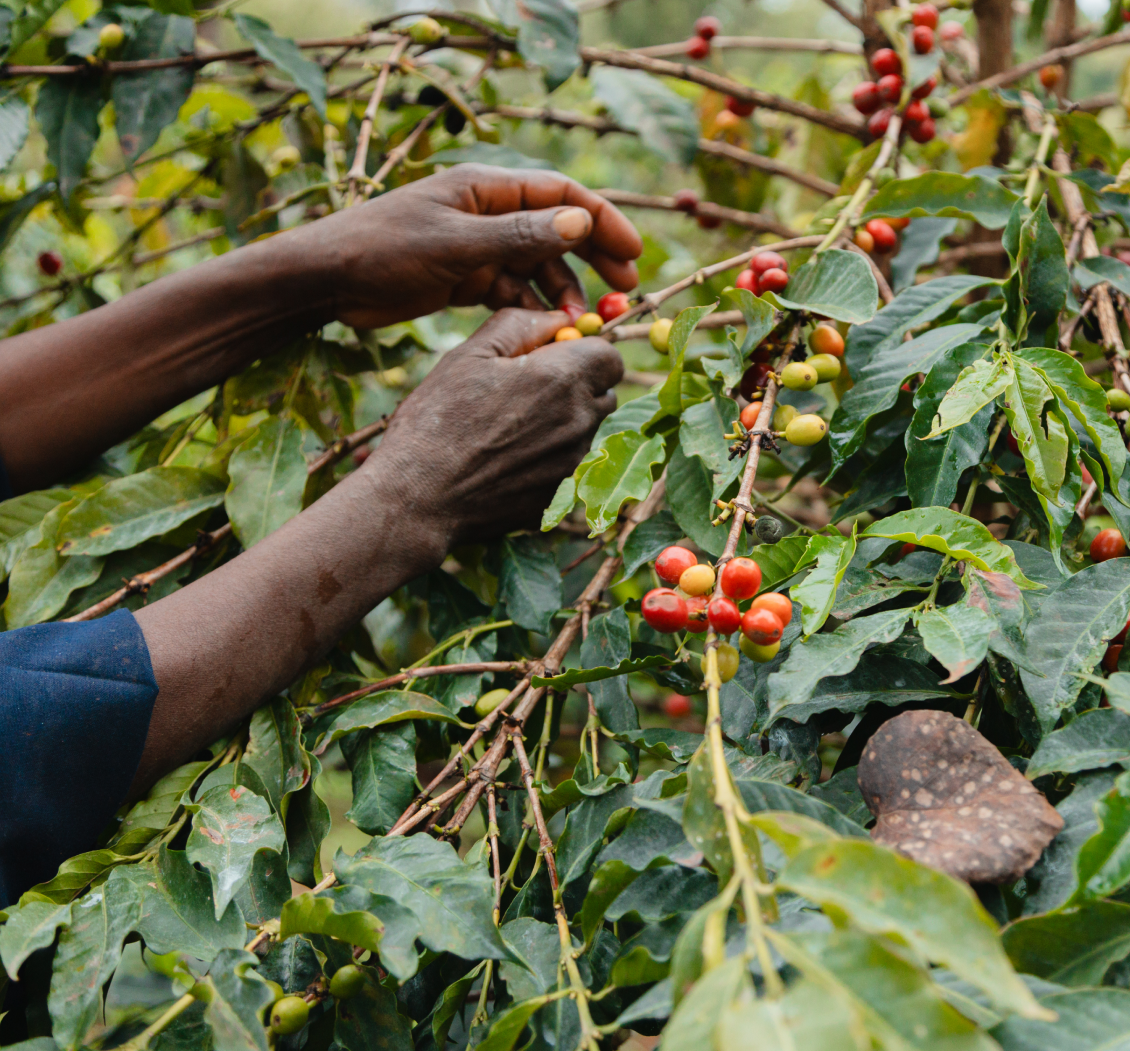
FUCO valuechain
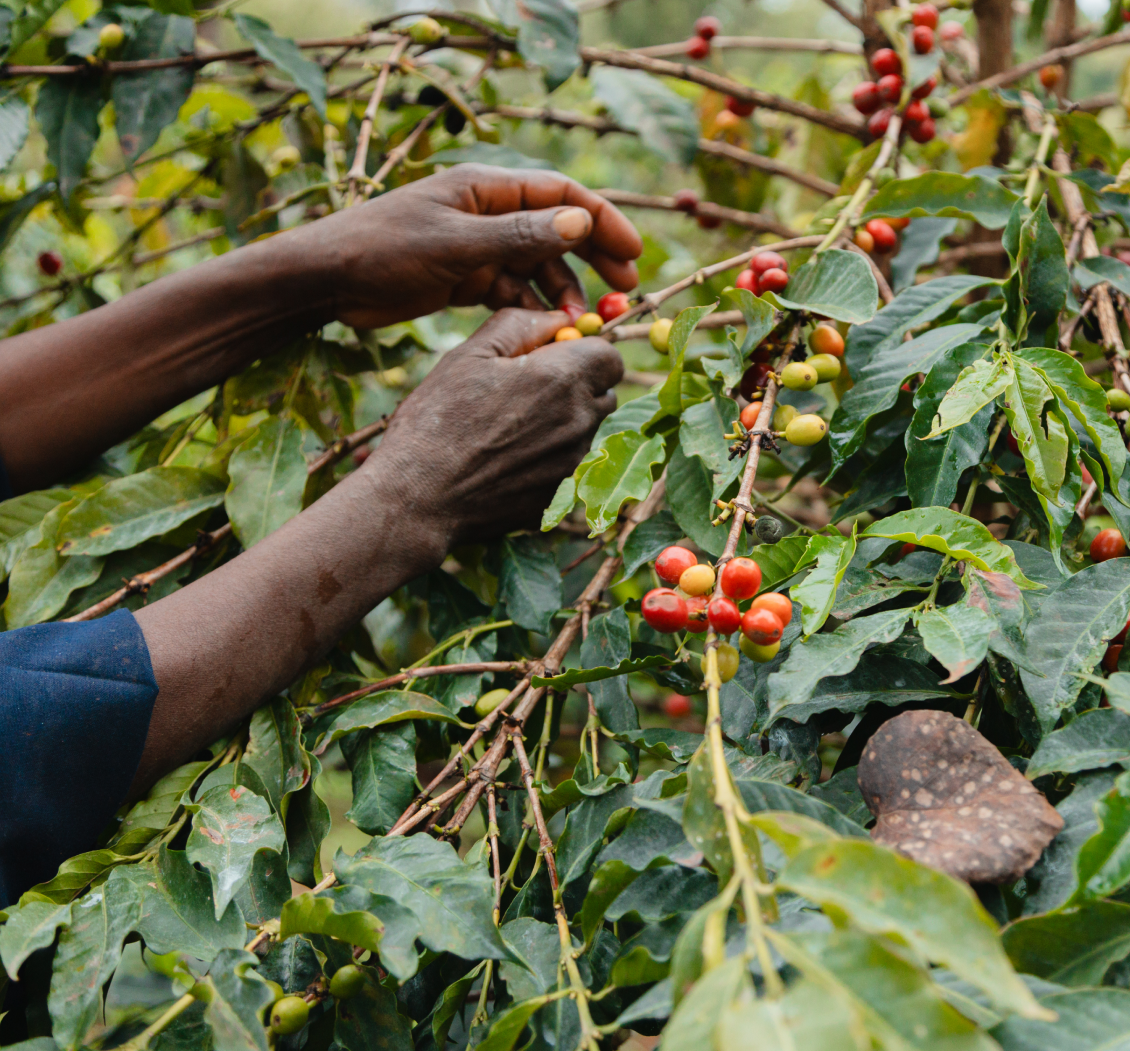
Step 1: Origin & Sourcing - Where It All Begins
We know our farmers. Period.
At FUCO, everything starts with one condition: we must know exactly where our coffee comes from. Not ‘roughly’ or via some label. We mean really know.
We only work with cooperatives, farmers, and exporters we know personally—relationships built over years. People who not only deliver quality but also understand that good coffee is only truly good when the entire process is right.
No label madness. Just clarity.
Fairtrade, Rainforest Alliance—it’s fine if you need it. Our partners often carry them. But we prefer to trust what we see, hear and experience ourselves.
We travel to origin. Always. To Kenya, Brazil, Peru, Colombia. Not for the photo (though we do take some), but because only on-site can you really see how people work and whether there’s a future in what they do.
Quality is the key. For everyone.
We buy only top-quality coffee, known in coffee terms as specialty coffee. Why? Simple: the higher the quality, the better the price for the farmer. That’s why we invest together with our partners in what’s needed to get there. Think: better farming techniques, smarter use of scarce resources like water and fertilizers, and adapting to a changing climate. Great coffee doesn’t just happen. It takes work. Together.
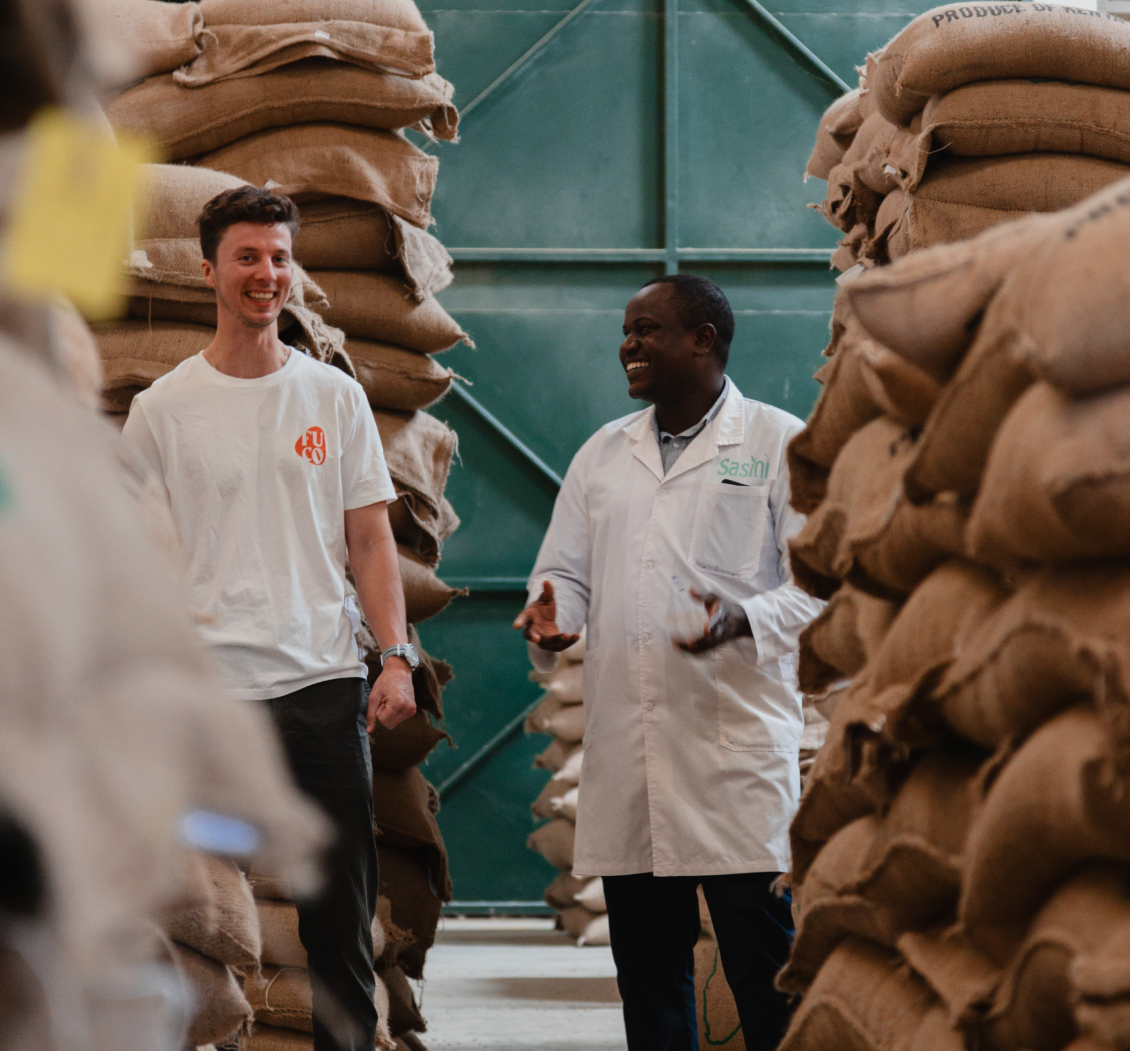
Step 2: Purchasing & Logistics – The Road to Reliability Starts at the Port
Good coffee doesn’t end in the field.
It has to arrive well too: fresh, safe and on time. That’s why FUCO doesn’t just control origin, but also everything after: transport, storage and logistics.
No loose ends in the chain.
Once the coffee leaves its country of origin, our logistical chain kicks into gear. No anonymous bulk channels, but fixed routes and familiar partners.
FUCO works with trusted shipping lines we’ve selected for their quality, reliability
and transparency. We know who loads the container, when it leaves, what route it takes and who unloads it. Short lines. No noise.
Antwerp as our fixed anchor point.
We’ve worked with the same storage partner in the port of Antwerp for years. Not because we have to, but because it works. They understand our volumes, our quality standards, and our pace. Every shipment is checked immediately upon arrival and prepared for further distribution. The result: minimal delay, maximum freshness.
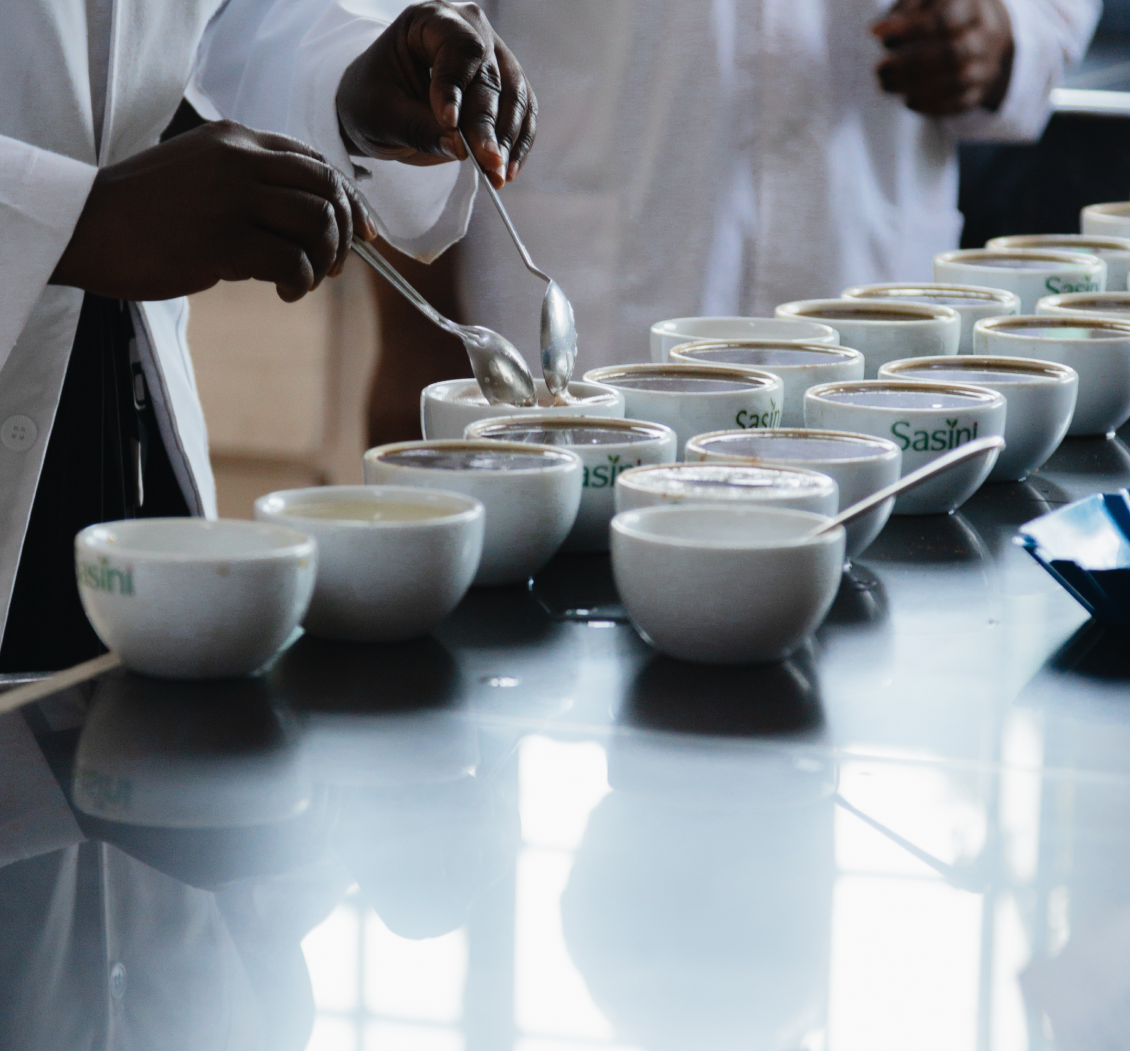
Step 3: Roasting – Roasting Without Interference
Flavor is forged in fire.
Coffee’s taste isn’t determined solely by origin. It’s also created in the roast—where the bean gets its character. So we don’t outsource that. Not to third parties. Not to bulk roasters. Every roast is done under the supervision of our own team, according to our own profiles.
Craft in our own hands.
All roasting is done manually by the FUCO team, without any external roasters involved. We write our own roast profiles, cup every batch, and fine-tune as needed. That means: full control over temperature, time, air pressure, and taste—from start to finish.
Technology that doesn’t sacrifice impact.
We roast on a Loring machine, chosen for its ultra-low emission profile. This system uses internal heat recovery and after burning of exhaust gases, resulting in significantly lower emissions compared to conventional systems. With 30kg batch sizes, we roast efficiently and at scale—without overcapacity or waste. Those who roast themselves set their own standards. And we do, every single batch.
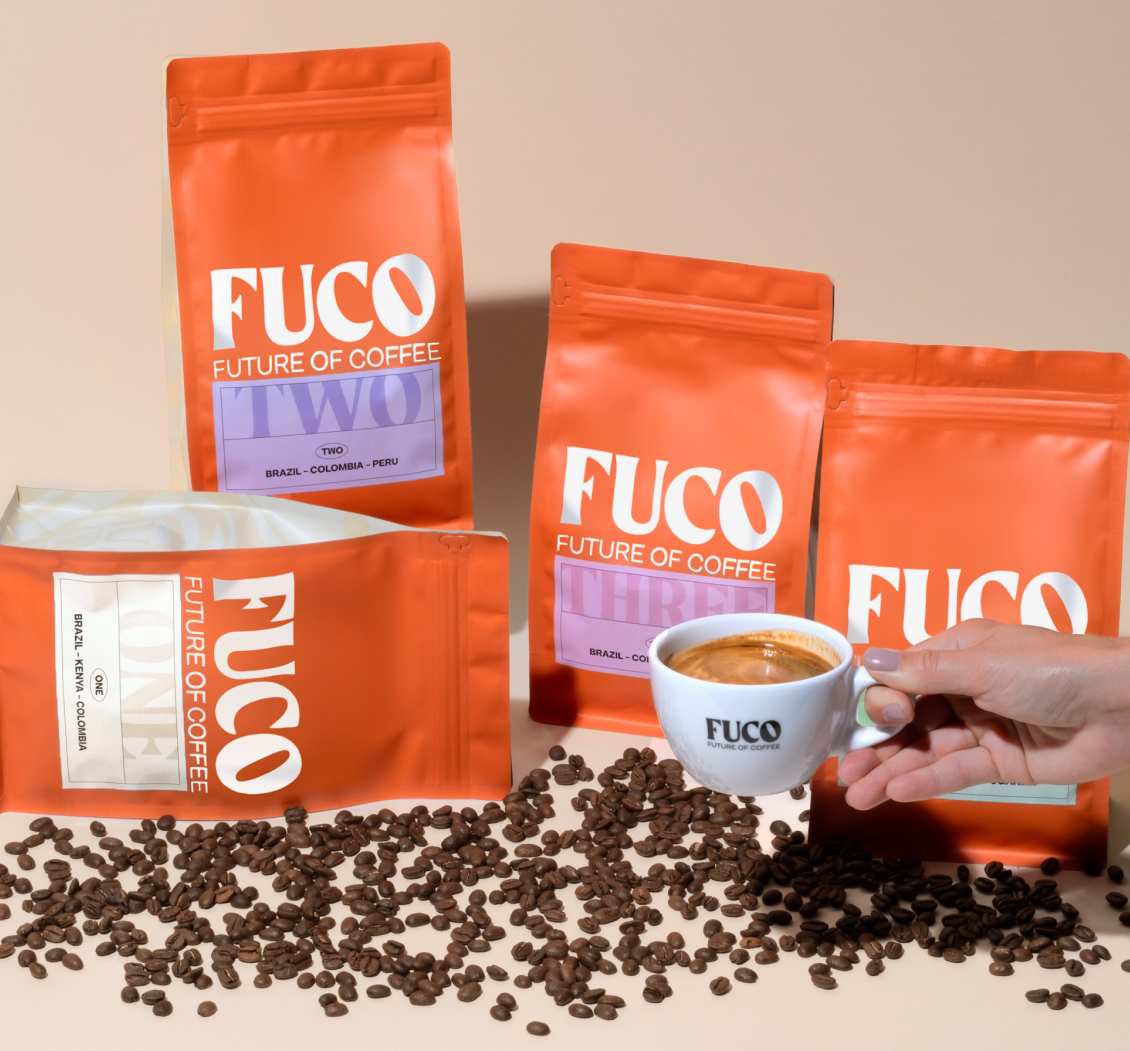
Step 4: Packaging – Protection Without Collateral Damage
Packaging is more than a bag.
It’s protection, presentation and responsibility in one. That’s why FUCO doesn’t go for the cheapest option—but the smartest one.
What’s inside matters. What’s around it too.
Our packaging is fully recyclable. It’s produced in Europe—not halfway across the world. That significantly reduces emissions, especially compared to production and shipping from Asia.
Plus, it meets strict EU regulations on food safety and materials. No junk. No empty claims. Just good stuff.
For business clients: return, refill, repeat.
For B2B clients: offices, hospitality, caterers. We also offer reusable coffee containers. Empty container returned? Full container delivered. That way, we reduce packaging waste, cut down on transport packaging, and keep the chain streamlined. Fewer packaging miles. Less waste flow.
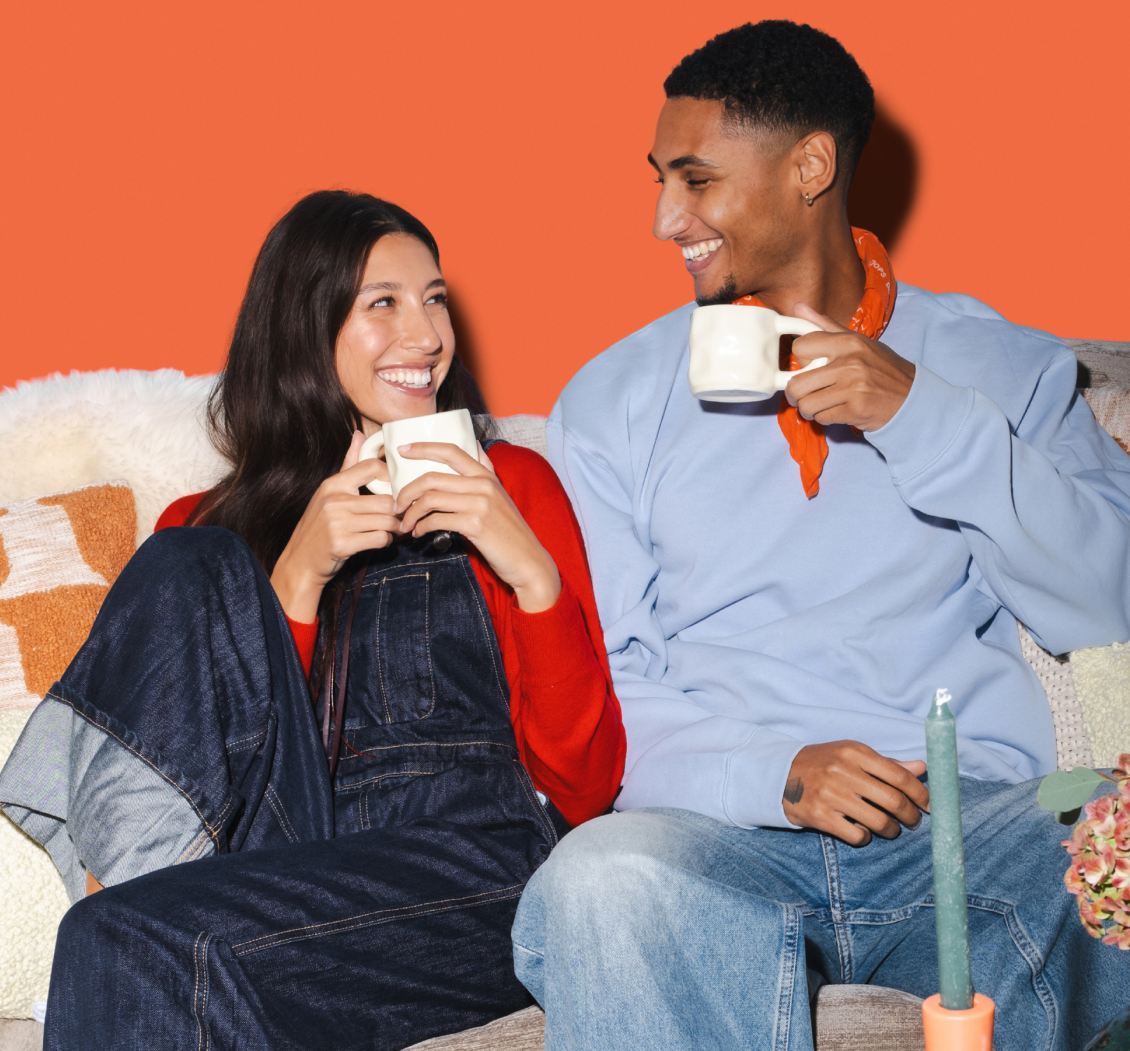
Step 5: B2B Delivery – Shipping Without Emissions
The last step is the most visible.
Once the coffee is roasted and packed, it simply has to arrive—on time, in perfect condition, no hassle. So we manage this ourselves too, with the same level of control as all steps before.
Our own van, our own plan, our own responsibility.
In many cases, we deliver using our own electric delivery van. No third-party couriers. No diesel vans wrapped in greenwashing. Just quiet, emission-free deliveries by our own team. We drive ourselves whenever we can—especially in the Randstad—because we know that reliability starts with controlling the last mile.
Sustainability without middlemen.
By delivering ourselves, we align delivery times with both customer convenience and efficiency. No half-full trips. No unnecessary kilometers. For customers, this means less waiting, predictable delivery, and direct communication. For us: lower emissions, lower transport costs, more control.